Remote Managed Inventory
Browse Inventory Management Options
Many Swagelok customers are in heavy asset industries and have applications involving high pressures, high temperatures, and/or difficult chemistry. In these environments, having certain components on hand is key. As a video below on this page shows, advanced stocking and kitting can help expedite production. Scroll down to review options. In a hurry? Please call 510-933-6200.
Auto Replenishment
Swagelok Northern California can enter orders for replenishment products into our customer's purchasing systems and/or periodically visit their facility to replenish their inventory. We can also provide reports with data such as total cost savings.
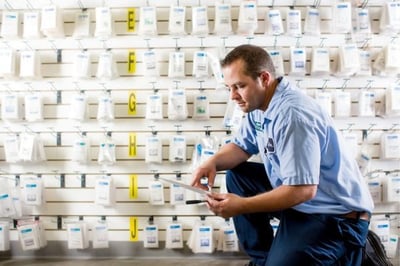
Collaborative Forecasting
Customers can link their forecasts with our fulfillment system to help ensure a steady supply of Swagelok components. We analyze a customer's historical and projected product usage to ensure high fill rates while avoiding carrying costs associated with overstocking.
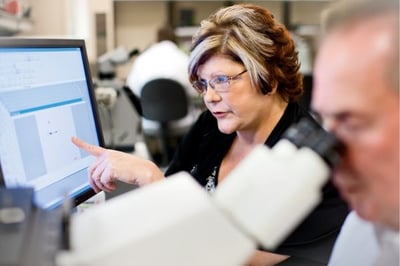
Custom Kitting & Packaging
We can package components to our customer's specifications. For example, we can double bag components in our Class 100 Clean Room; bundle components; tag/label parts, and more. Such options can save valuable time over days, months, and years; cuts down on packaging waste, and more.
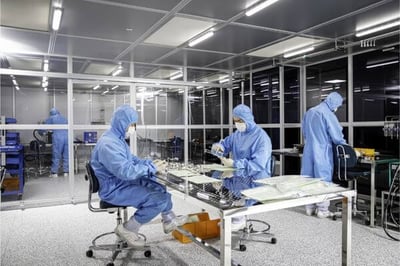
Remote Managed Inventory
RMI can provide savings by reducing stocking levels, which lowers carrying costs. It also helps reduce transaction costs (i.e. ordering, cycle counting, receiving). We help analyze current usage and identify minimum and maximum levels for inventory. Put our team alongside yours to manage your inventory.

About Swagelok Northern California
Since 1963, Swagelok Northern California has provided thousands of manufacturers, processors, suppliers, and innovators with Swagelok fluid system products and expertise. Over 100 engineers, technicians, trainers, and other professionals make up our local team. With that expertise and $25M worth of Swagelok products in our three local warehouses, we are ready to help you run safe, cost-effective operations.
About Swagelok Company
Established in 1947, Swagelok Company is a global company headquartered in Solon, Ohio. It has 20 manufacturing facilities, 6 global technical centers, and a network of 225 sales and service centers in 70 countries employing thousands of associates.
Request Information/Support
Need details or a quote? We are ready to help.