Gas distribution systems are widely used in California industrial facilities within industries including petrochemical, semiconductor, and biotechnology. Gas distribution systems typically consist of four subsystems:
- Source inlet connection
- Primary gas pressure control (gas control panel)
- Point of use
- Automatic changeover
The system as a whole must safely and effectively deliver gases from a high-pressure source to the point of use at a specific pressure and flow rate. Gas control panels are the first stage of management of high-pressure gases and act as the primary pressure control point and thus, should be given special consideration.
Below, our gas panel design guide details the basics of gas control panels and top considerations when seeking a replacement or new panel for a gas distribution system.
Gas Panel Design Guide: The Basics
Gas panels—the primary pressure control point in gas distribution systems—are located near the gas source (gas cylinder). Gas control panels reduce the pressure from the cylinder to deliver the gas to the next stage of the gas distribution network at the correct pressure and flow rate, where it is then delivered to the point of use.
The point of use can range from analyzers to process equipment to laboratories depending on the particular application. Below, is an example of how gas panels can be incorporated into a gas distribution system for an analytical instrumentation shelter.
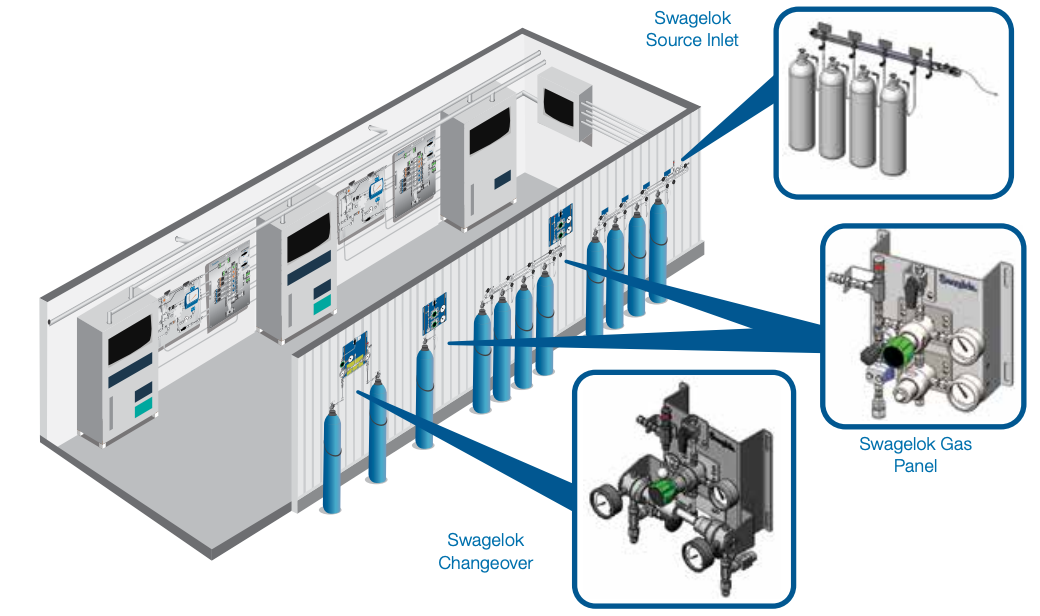
Gas panels reduce pressure from the cylinder via either a single-stage or dual-stage pressure regulator arrangement. Careful selection and sizing of pressure regulators are paramount to maintain a properly functioning gas distribution system.
Gas Panel Design Guide: Top Considerations
When looking to install a new gas control panel for a gas distribution system, there are several important considerations that can help ensure:
- The gas is properly reduced to the specified pressure and flow rate
- The panel is easy to install, operate, and maintain
- Safety regarding facility employees and the environment
- Reliability to minimize downtime
Pressure Regulator Considerations
The most important factor for an effective gas control panel is the proper selection of a pressure regulator. To understand how to make this selection, it is important to understand these four aspects of pressure regulator performance:
- Droop: the “flat” middle section pictured in the below flow curve is actually non-linear and slopes downward—this is known as droop. Depending on the pressure regulator selected, the outlet pressure will drop by some degree as flow demand increases.
- Seat-load drop and lock-up: the small first section of the curve (pictured: from left to right) demonstrates seat-load drop and is the initial pressure drop experienced when a regulator starts from a zero flow condition. If looking at the same section of the curve from right to left, this is known as lock-up, characterized by an increase in outlet pressure as flow is decreased to zero.
- Choked flow: the steep negative slope on the far right side of the below curve demonstrates choked flow. This occurs when the flow demand is greater than the pressure-controlling capabilities of the pressure regulator.
- Supply-pressure effect: this effect is characterized by the change of regulator pressure as a function of change in inlet pressure.
Below is a typical flow curve for a pressure-reducing regulator which demonstrates the above aspects.
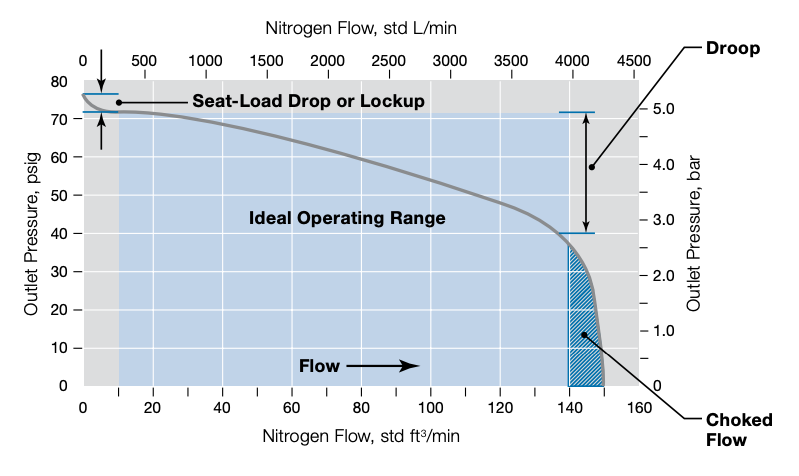
Single-stage pressure regulators reduce cylinder gas pressure within a determined range in one step, while dual-stage complete this process in two steps.
The above aspects of regulator performance vary between single-stage and dual-stage pressure regulators. For example, single-stage pressure regulators typically show minimal droop with varied flow rates but may show a high supply-pressure effect. On the other hand, dual-stage pressure regulators may typically show minimal supply pressure effects but may show a steeper slope in droop. To properly determine the correct regulator and sizing, it is required to calculate the correct gas pressure and flow rate.
Single-stage
|
Dual-stage
|
Proper Calculation of Gas Pressure and Flow Rate
A wide range of gases is used in gas distribution systems within the petrochemical, semiconductor, and biotechnology industries. Common gases include hydrogen, nitrogen, carbon dioxide, oxygen, helium, argon, and propane, and exotic gases such as bromine, titanium tetrachloride, and phosphorus trifluoride. The calculation of flow rate and pressure depends on the gas type and several process aspects. This calculation is critical for proper pressure regulator and gas panel functionality. A fluid systems expert should be consulted to assist with this calculation and ensure the proper pressure regulator is selected.
Utilizing a custom gas control panel design specific to applications can reduce the likelihood of leaks and ensure ease of operation and maintenance. Leaks are often the result of an excessive number of connections. Noting that every connection should be treated as a potential leak point, specialty fittings and connectors can be used to eliminate extra connections, thus minimizing the number of potential leak points in the design. Leaks often mean wasted money for industrial facilities in addition to being a safety hazard when toxic gases are being distributed.
An intuitive and clearly labeled panel can promote proper operation and minimize the risk of operator error. Panels designed in a modular manner are easily serviceable when maintenance is required, minimizing downtime.
Components and Instrumentation
Implementation of a standardized, yet configurable, backplate allows for the plate to work with standard cylinder sizes and meet configuration requirements as deemed by specific applications. Gas control panels should include pressure indicators upstream and downstream and can include:
- Relief valves
- Ball valves
- Non-rotating stem needle valves
- Tubing and fittings
Depending on the application, type of gas, and operating conditions, materials of construction may vary.
Operator and Environmental Safety
When delivering gases that may be harmful to operators and the environment if a leak occurs, it is important to mitigate safety risks to ensure operator safety and prevent potential sanctions. While catastrophic leaks are rare, restricted flow orifices can be placed near the gas source, thus limiting the maximum flow rate and providing an additional level of protection.
Temperature and pressure ratings for components within a gas panel must align with process requirements to ensure safe operations. Additionally, components, such as valves, may have the same rating but one may be better suited for a specific application. Pressure regulators, as well as pressure relief valves, should be sized to accommodate the full range of potential flow rates and pressures.
Reliability
As gas distribution systems play an important role in industrial facilities and gas control panels are the primary pressure control system, the reliability of gas panels is critical. Unreliable gas panels can affect equipment, processes, or laboratories which rely on the gas distribution system to deliver a particular gas. This may result in damage to equipment or maintenance resulting in downtime for various processes in industrial facilities. Throughout the lifecycle of gas distribution systems, reliable gas panels should prevent leaks and wear on components and deliver gas within the correct flow rate and pressure ranges required for a given application.
Supporting Future Changes in Process Conditions
Process conditions for many industrial applications are likely to change over time. Thus, designing to accommodate such future changes can prevent the need to swap out or modify existing pressure control components down the line. Pressure control components, including relief valves and pressure regulators, can be sized to support a wider range of flow rates and pressures, providing flexibility to meet future process conditions. However, sizing pressure control components to support too wide of a range may result in poor performance within the most important range. Consequently, careful consideration is required to properly size pressure control components to maintain high performance within the most important range of pressures and flow rates while also accommodating conditions outside of that range.
Your Local Gas Panel Designer and Fabricator: Swagelok Northern California
Safe and effective distribution of high-pressure gas to end-process applications—at the correct pressure and flow rate—depends heavily on the utilization of a properly designed gas control panel. Whether you are looking to replace an existing gas panel or standardize panels across a facility, Field Engineers at Swagelok Northern California can perform a detailed assessment of your gas distribution requirements to design and fabricate a gas control panel suited for your application.
With over 50 years of experience supporting the needs of the petrochemical, semiconductor, and biotechnology industries in Northern California, our Field Engineers have a deep understanding of local applications. Beyond our gas panel design guide, we can provide custom-configured designs fueled by best practices. Swagelok gas panels come fully assembled and are tested prior to delivery to ensure ease of installation. All gas panels and other subsystems are backed by our industry-leading Lifetime Warranty.
To find out more about design considerations beyond this gas panel design guide and how Swagelok Northern California can help design a custom-configured gas control panel, contact our team today by calling 510-933-6200.