Swagelok Onsite Services
Browse Onsite Services
We offer Swagelok field engineers who can identify the root cause of current fluid system issues and advise on repairs. We advise on changes to improve system efficiency and head off future repairs. Need details or a quote? Please click above or call 510-933-6200.
Compressed Gas Leak Detection
Swagelok engineers detect leaks, identify their cause, quantify their cost, and specify how to tighten up. See the cost of each leak, calculated by looking at a leak's effect on energy costs, system reliability, safety, and other factors. Take action and save.
Fluid System Evaluation
Bring the applications experience of Swagelok field engineers to your facilities. They conduct a thorough evaluation of fluid systems and provide detailed findings to help optimize operational performance, mitigate a variety of risks, lower energy costs, and save time.
Gas Distribution Program
Swagelok pressure control specialists can evaluate the efficiency and safety of a customer's gas distribution system, report in detail on the root cause of issues, and advise on steps to take to lower energy costs and improve reliability.
Hose Advisory & Optimization
Swagelok field engineers inspect installed hose, gather information about routines and costs related to hose, and provide detailed guidance on how to make hoses perform better and last longer — including a hose register update (or new database).
Sampling System Evaluation
Our field engineers document existing systems, looking for ways to eliminate causes of poor sample quality, such as blockage or moisture carryover; reduce maintenance and analyzer downtime; resolve issues caused by high particulate loads; and more.
Steam System Audit
Find out where a plant is losing energy with a thorough steam system audit. Our experts conduct a detailed assessment of the customer's steam systems and components, document and tag areas needing attention, and advise on steps to repair and optimize.
Technical Support
Our technical support team can provide Swagelok part selection support, help configure products like a pressure regulator or valve, and much more. (For urgent issues outside business hours, call 510-933-6200 and follow "emergency service" prompts.)
Virtual Option
Many Swagelok advisory services can be provided via phone, video, file exchanges, and the like. Among other things, we can evaluate P&ID’s for functionality and suggest products or alternatives; evaluate models to advance design work/simplify layout; and more.
Work with Top Fluid Systems Engineers
Helping your team find, address, and prevent fluid system issues.
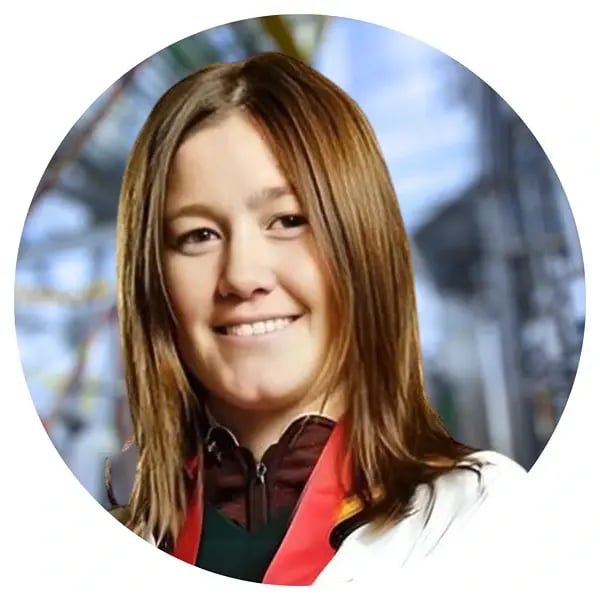
Stacey Phillips, MEng, has worked alongside hundreds of Swagelok customers over 18 years.
- As Swagelok Northern California Director/General Markets she helps teams effectively manage hydrogen, improve plant operations, save on equipment assembly, make process fluid sampling reliable, and keep systems running for semi fabrication.
- Previously, she served as Swagelok Field Engineering Manager/Americas. Your team can rely on her expertise in pressure control, process instrumentation and automation, valve selection, grab sampling, extending the life of rotating equipment, and more.
- Earlier, she built a thriving Swagelok Custom Solutions practice in Canada. "In the early days, I would give a quote for equipment, then go in the back and build it," she says. That meant CAD design, building enclosures, configuring instrumentation, testing—whatever was needed.
Stacey holds a Master of Engineering (MEng) from University of Colorado, Boulder and a Bachelor of Science (BSc), Biomechanics from University of Alberta.
Pairing Onsite Services and Assembly Services
Customers get extra value when they use both our Onsite Services and Assembly Services.
During an onsite evaluation, a Swagelok field engineer gathers data on your existing, installed systems and delivers detailed information on how to improve it.
If you like, our team can go a step further and advise on using a Swagelok custom solution to solve a problem. We are glad to estimate the savings and other benefits from a custom solution, and handle fluid system design and assembly if you opt for it.

Examples
Swagelok field engineers can address almost any fluid system issue.

Diagnosing Hose Installation Errors
Problem—A local manufacturer experiencing production slow downs called in Swagelok Northern California field engineers for a system evaluation.
Root cause analysis—Our team zeroed in on a system handling both supply and return in a cooling media assembly. The supply and return hoses looked almost identical, and that was leading to numerous hose installation errors — even by their most experienced technicians.
Solution—Swagelok gave hose a unique type of connection, so it became physically impossible for technicians to reverse the supply and return components. Production sped up. Labor costs for rework dropped.
.jpg?width=600&height=400&name=Design%20Consulting%20(3).jpg)
Pinpointing the Root Cause of Bad Data
Problem—A customer who was experiencing longer-than-anticipated response times on its analyzer called in Swagelok field engineers. Our team performed a system evaluation.
Root cause analysis—Fluid was changing phase multiple times as it traveled from tap to analyzer. Phase changes in a sampling line can deliver a sample to the analyzer that is not representative of the process, and as a result, the customer was making process changes based on inaccurate analytical data.
Solution—With Swagelok's help the customer eliminated all phase changes, improved its response time, and ensured representative results.
Swagelok Engineering Advantage
Celebrating 75+ years.
Subject Matter Experts
Our field engineers earn certification by completing hundreds of training hours with internationally renowned experts and passing dozens of exams. They also recertify every three years.
Global Network
Our local field engineers are part of a network of 100+ Swagelok field engineers around the world. They consult each other for specific applications experiences and more.
Broad Capabilities
Our local team includes engineers, tech support gurus, assembly technicians, procurement experts, and more. We strive to integrate all our capabilities to deliver total solutions to you.
Quality first
Fast and flexible
Passion for details
Award-winning team
Always reachable
Easy start


About Field Engineers
During training, each field engineer completes hundreds of hours of live instructor-led training and dozens of exams. Over the course of one year, candidates must attend weekly classes and achieve virtually perfect scores on every test to advance.
Program pre-requisites
A trusted brand stands behind each Swagelok field engineer. Swagelok is a $2.4B company founded in 1947. Our quality management systems, values-driven people, and high quality products combine to help ensure consistency and value.
To start training for certification as a Swagelok Field Engineer, an engineer must have experience designing systems for diverse applications, optimizing systems to increase operator safety and decrease operating costs, and working with numerous OEM plant systems and equipment packages.
During training, each field engineer completes hundreds of hours of live instructor-led training and dozens of exams. Over the course of one year, candidates must attend weekly classes and achieve virtually perfect scores on every test to advance.
Continuing education
Swagelok field engineers must re-certify at intervals. And they may pursue additional certifications, such as the Certified-SSEAS and Certified-FSEAS badges. The additional training prepares our field engineers to seamlessly deliver total solutions for customers, every time.
Swagelok and Swagelok Northern California have low turnover, so our local field engineer who learns about your systems and applications may be just a phone call away for years to come.
No-risk next step
Thousands of companies have benefited from collaborating with Swagelok field engineers. Having a conversation with a senior member of our team about your options creates no obligation or costs. Please give us a call at 510-933-6200.
About Us
Learn about Swagelok Company and Swagelok Northern California
Since 1963, Swagelok Northern California has provided thousands of manufacturers, processors, suppliers, and innovators with Swagelok fluid system products and expertise. Over 100 engineers, technicians, trainers, and other professionals make up our local team. With that expertise and $25M worth of Swagelok products in our three local warehouses, we are ready to help you run safe, cost-effective operations.
Established in 1947, Swagelok Company is a global company headquartered in Solon, Ohio. It has 20 manufacturing facilities, 6 global technical centers, and a network of 225 sales and service centers in 70 countries employing thousands of associates.
Request Information/Quote
Need details or a quote? We are ready to help.