While semiconductor manufacturing is a complex industry from both a technical and business perspective, most semiconductor fabrication challenges arise from the supply chain. In 2020, we saw the beginning of a major chip shortage that impacted multiple industries and continues to be felt globally. Supplies of goods ranging from computers and smartphones to cars have been disrupted by the ongoing shortage.
With only a handful of major chip manufacturers in the world, the semiconductor industry is uniquely dependent on global supply chains. That means your relationships with your vendors and suppliers are critical to maintaining smooth operations. Time, cost, performance, and innovation are some of the biggest semiconductor fabrication challenges manufacturers must face, and it is important to partner with suppliers who will work with you to help minimize risk.
Time
Semiconductor demand, driven by new technologies like 5G, artificial intelligence, and the internet of things (I-o-T), is growing at least as quickly as planned capacity. Meeting the market’s needs requires a supplier that can deliver critical systems and components quickly. You need a local supplier with the experience and knowledge to solve problems in a timely manner and keep up with demand.
Reliability is critical when it comes to meeting production schedules. Much of the critical production equipment used in semiconductor fabs runs continuously, so it must be reliable and easy to service to minimize downtime.
Piping and tubing are especially critical parts of the semiconductor manufacturing process that are often overlooked. The ultra-high-purity (UHP) piping in a semiconductor cleanroom must distribute process gases at required flow rates and temperatures while keeping out environmental impurities that can interfere with production. Minor problems in process piping and tubing, like weld defects, can ruin an entire batch. Even small defects can require significant repairs that lead to delays. It is worth investing in high-quality UHP piping and tubing from a vendor that meets the required standards.
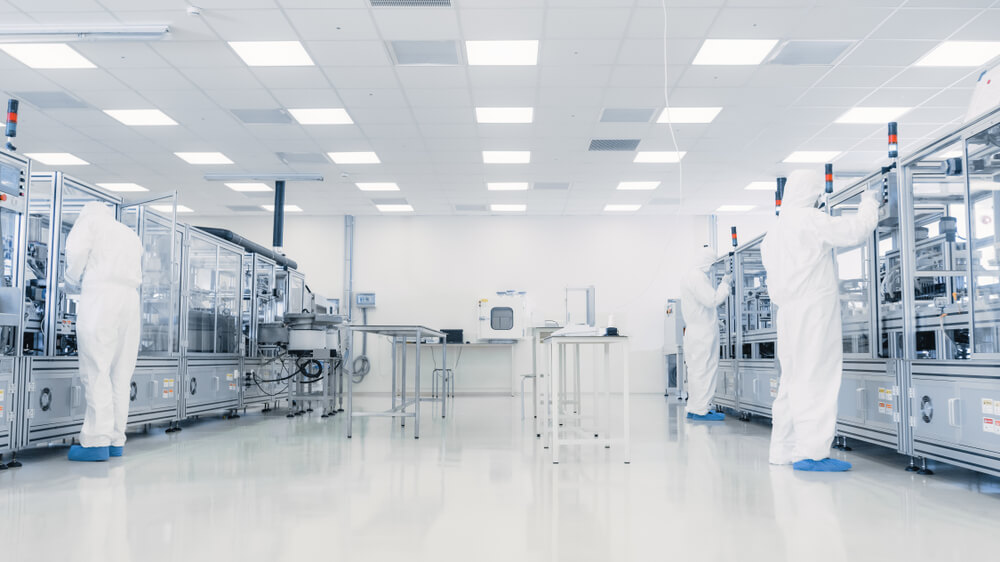
Ideally, manufacturers, OEMs, and suppliers could engage in real-time information exchange, allowing the entire supply chain to react quickly to changes in supply and demand. However, this capability is not common, so it falls on supplier-customer contacts to communicate early and often to avoid bigger semiconductor fabrication challenges down the line. Even small shifts in demand can cause production planning volumes to fluctuate in response (the “bullwhip effect”).
Staying on top of semiconductor demand and manufacturing trends requires good communication between customers and suppliers. By working closely with their customers, chip companies have a better idea of future demand, reducing the bullwhip effect from demand swings. Likewise, collaborating with suppliers via synchronized capacity planning can mitigate supply risks and allow more reliable production planning.
Cost
As production costs rise, the semiconductor industry is being forced to adopt leaner manufacturing practices. This typically means buying later and keeping inventory buffers low; however, there is such a thing as too lean. The current chip shortage demonstrates the inherent risk in this strategy. Manufacturers must find a middle ground between stockpiling inventory and just-in-time production.
However, with the importance of quality and the growing demand for semiconductors, lean manufacturing can only go so far. To ensure long-lasting, reliable performance from your fabrication equipment, you need quality systems and components with predictable lifecycles. Cheaper parts may cost less upfront, but the added repair and replacement costs quickly add up. Plus, the last thing you want is an equipment failure that leads to lost time and production. The best way to avoid costly surprises is by sourcing the highest quality products available backed by the best warranty in the industry.
Another way to cut costs is by bringing maintenance and repair operations in-house. Orbital welding training, for example, allows you to quickly train personnel to create high-quality welds on piping and tubing. Though it requires an initial investment in equipment and training, the cost is minimal compared to the long-term savings of having in-house personnel trained in orbital welding.
Performance
Designing and implementing a cooling system in a semiconductor manufacturing environment can be a challenge. The high-precision processes of modern, high-performance semiconductor production require very precise thermal management. These processes generate high thermal demand, which your cooling equipment needs to be able to handle.
When designing a thermal management system for semiconductor fabrication, challenges include material compatibility, valve control, cleanliness, space optimization, compliance, and ease of maintenance. All these factors affect the total cost of ownership and must be considered when selecting systems and components to create an optimized process. Communication and collaboration with your vendor are essential, as they can identify the exact components and systems needed for the process and the manufacturing environment.
Cutting-edge thermal management solutions, like pre-insulated hoses and tubing, ensure you get optimal heater and chiller performance. High-quality thermal insulation is critical to reducing heat transfer from process piping and tubing in controlled cleanroom environments.
Electropolishing is essential for creating a smooth inner surface for gas delivery systems to prevent corrosion. Electropolishing is superior to mechanical polishing for semiconductor applications, as no abrasives are left behind as with mechanical polishing. Additionally, this process results in a smoother wetted surface and reduced wetted surface area, which improves dry-down and system purge times.
Innovation
The market for semiconductor products is moving faster than ever. Almost every product you can think of contains semiconductors—which means the demand for smaller and more powerful chips won’t be slowing down any time soon.
What would happen if semiconductor companies fail to innovate and evolve along with new technology? If semiconductor performance doesn’t keep up with growing performance demands, chip speed and affordability will slow over time, and semiconductor devices will eventually stagnate as they reach the limits of Moore’s Law. Given the semiconductor fabrication challenges that arise from the fast pace of technological change, it’s no wonder the industry invests so heavily in R&D.
Rapidly evolving technology is also forcing semiconductor manufacturers to rethink their supply chains. Typically, fabricators, vendors, testing companies, equipment makers, and other parts of the supply chain face semiconductor fabrication challenges individually. Often, communication between parties is poor or comes too late in the project to be effective.
To reach higher operational standards while improving quality, cycle times, and revenue, a smarter, more holistic view of the manufacturing process is needed. Semiconductor manufacturing is complicated, largely automated, and expensive. Fabricators, OEMs, and vendors can all gain by partnering to apply advanced analytics to make processes faster and more efficient. Even without advanced analytics, collaboration on semiconductor fabrication challenges and project timelines makes everything run more smoothly.
Tackle Semiconductor Fabrication Challenges with Help from the Experts
Swagelok has the experience and expertise to help you take on even the semiconductor fabrication challenges. We offer the highest quality components, including industry-leading valves and tube fittings, to ensure your operations are at the highest level of safety and efficiency. Our expert Field Engineers can provide consultation on incorporating components into existing systems or setting up new ones.
Our locations in Northern California allow us to serve the regional semiconductor industry by quickly delivering components and dispatching experts to troubleshoot as soon as problems arise. Furthermore, Swagelok’s limited lifetime warranty assures you’re getting quality backed by the best warranty in the industry.
To find out more about how Swagelok Northern California can help you with semiconductor fabrication challenges, contact our team today by calling 510-933-6200.