Identifying and solving mechanical seal and seal support problems doesn’t have to be guesswork especially if you’re new to the complexity of refinery processes. The diversity of centrifugal pumps, their process applications, and mechanical seal support systems can be overwhelming. Even with the dozens of mechanical seal support system configurations (API 682 Plans, as they’re known in the industry), a methodical approach to troubleshooting can help isolate and resolve the problem more efficiently.
Based on my years of working with maintenance personnel in Bay Area refineries, I’ve summarized below in tables and bullet points a quick mechanical seal support troubleshooting guide.
Have There Been Changes in Process Conditions?
The first question I always ask, especially in Bay Area refineries that have been operating for decades—with infrastructure and processes designed for crudes that were predominant years ago—is: Have there been changes in process conditions that could impact the reliability of the mechanical seal and seal support system? Some of the process changes that many require corresponding changes to mechanical seals and their support systems include:
- Transitioning from sweet crude to a sour crude with higher H2S concentrations
- Higher temperature process fluids that exceed the rated capacity of the mechanical seal or seal support system (prolonged, excessive temperatures eventually lead to mechanical seal failure)
- Increased upstream pressure is not properly compensated by the pressure of barrier fluid supplied to dual mechanical seals, resulting in process fluid migration across the inboard seal, undermining mechanical seal integrity leading to process fluid leakage
- Decreased upstream pressure is not properly compensated by the pressure of buffer fluid supplied to dual mechanical seals, resulting in buffer fluid migration across the inboard seal, potentially contaminating the process fluid
- Increased particulates in the process fluid are fouling orifices and valves and preventing the proper flow through the seal chamber
Process changes don’t always result in an immediately recognizable problem. But you can avoid potential problems by making sure that any changes to pumping process parameters—fluid composition, temperature, or pressure—are checked against the rated capabilities of the pump, mechanical seal, and seal support system.
An experienced mechanical seal and your local seal support system vendor can provide the guidance to help troubleshoot problems that are the result of changing process conditions. A change of mechanical seal type or design or an upgrade of an existing mechanical seal support system is often the fast path to reliability.
Mechanical Seal Support Troubleshooting Guide
Now that I’ve cautioned you on process changes that can cause trouble, let me focus on troubleshooting the problems associated with seal support system functions. In this section, I’m assuming the mechanical seal and seal support system have been correctly matched to the pumping conditions. Any single problem can have multiple effects on the support system, for example, a clogged orifice can reduce flow, pressure, and the ability to dissipate seal chamber heat.
I’ve structured this mechanical seal support troubleshooting guide, according to the most common categories—process side, dual seals, and atmospheric—for these systems.
Process Side Mechanical Seal Support Troubleshooting Guide
Process side seal plans deliver process fluid (API Plans 11, 12, 14, 21, 22, and 41), a compatible flush fluid (API Plan 23), or flush fluid from an external source (API Plan 32) to the seal chamber to lubricate the seal faces and maintain the proper seal chamber temperature and pressure for single seals. In the table below I’ve listed the most likely mechanical issues to look for when troubleshooting poorly performing seal support system plans.
Process Side Seal Support Issues
|
API Plan Number
|
|
11
|
12
|
13
|
14
|
21
|
22
|
23
|
32
|
41
|
Bent or pinched tubing
|
⚫
|
⚫
|
⚫
|
⚫
|
⚫
|
⚫
|
⚫
|
⚫
|
⚫
|
Incorrect pump discharge or suction orifice size
|
⚫
|
⚫
|
⚫
|
⚫
|
⚫
|
⚫
|
|
|
⚫
|
Leak at connection between tubing and discharge or seal chamber
|
⚫
|
⚫
|
⚫
|
⚫
|
⚫
|
⚫
|
⚫
|
⚫
|
⚫
|
Clogged strainer/filter
|
|
⚫
|
|
|
|
⚫
|
|
⚫
|
|
Improperly sized throat bushing
|
|
|
|
|
|
|
⚫
|
⚫
|
|
Damaged/inoperable pumping ring
|
|
|
|
|
|
|
⚫
|
|
|
Malfunctioning instrumentation indicates incorrect pressure, temperature, or flow
|
⚫
|
⚫
|
⚫
|
⚫
|
⚫
|
⚫
|
⚫
|
⚫
|
⚫
|
Inadequate flow of plant water through a heat exchanger
|
|
|
|
|
⚫
|
⚫
|
⚫
|
|
⚫
|
Scaling on heat exchanger cooling coils reduces thermal transfer efficiency
|
|
|
|
|
⚫
|
⚫
|
⚫
|
|
⚫
|
API Plan 32 - External Flush Fluid
This plan falls under the process-side category, but rather than using process fluid to maintain the proper seal chamber environment, API Plan 32 delivers a clean flush fluid into the seal chamber from an external source. That could be water, a water/glycol mixture, or oil-based fluid that is compatible with the process fluid.
When troubleshooting API Plan 32, look for an insufficient flow of external flush fluid (supply valve, depleted reservoir) and improper throat bushing clearance that allows too much flush fluid to migrate past the bushing into the process fluid. You don’t want to be using more flush fluid than is absolutely necessary.
These Options Can Make Maintenance Easier
There are a few other plan-specific things to consider to help permanently remedy frequently-occurring problems with process-side seal support systems. For API Plans 12, 22, and 32 that use a strainer or filter, including a bypass around the strainer/filter segment of the tubing can help eliminate any downtime associated with strainer/filter cleaning or replacement. And if the strainer/filter changes seem to be too frequent, you should consider upgrading to API Plan 41 which uses a cyclone separator to remove particulates.
Dual Seal Mechanical Seal Support Troubleshooting
Dual seal support systems circulate fluid between the inboard and outboard seals, providing a pressurized (API Plans 53A, 53B, 53C, 54 using barrier fluid) or unpressurized (API Plans 52, 55, 72 using buffer fluid) to maintain seal integrity and prevent leakage of process fluid.
Process Side Seal Support Issues
|
API Plan Number
|
|
52
|
53A
|
53B
|
53C
|
54
|
55
|
72
|
74
|
Bent or pinched tubing
|
⚫
|
⚫
|
⚫
|
⚫
|
⚫
|
⚫
|
⚫
|
⚫
|
Leak at connection between tubing and discharge or seal chamber
|
⚫
|
⚫
|
⚫
|
⚫
|
⚫
|
⚫
|
⚫
|
⚫
|
Low fluid level in seal pot or reservoir
|
⚫
|
⚫
|
⚫
|
⚫
|
⚫
|
⚫
|
|
|
Improper (low) barrier fluid pressure
|
|
⚫
|
⚫
|
⚫
|
⚫
|
|
|
⚫
|
Improper (high) buffer fluid pressure
|
⚫
|
|
|
|
|
⚫
|
⚫
|
|
Damaged/inoperable pumping ring
|
⚫
|
⚫
|
⚫
|
⚫
|
|
|
|
|
Malfunctioning instrumentation indicates incorrect pressure, temperature, flow, or fluid level
|
⚫
|
⚫
|
⚫
|
⚫
|
⚫
|
⚫
|
⚫
|
⚫
|
Inadequate flow of plant water through coils in seal pot reservoir or heat exchanger
|
|
⚫
|
⚫
|
⚫
|
⚫
|
⚫
|
|
|
Scaling on cooling coils reduces thermal transfer efficiency |
|
⚫
|
⚫
|
⚫
|
⚫
|
⚫
|
|
|
For each of these API plans, the buffer or barrier fluid must be chemically compatible with the process fluid. That may seem obvious, but I’ve seen situations where process fluid conditions have changed and barrier or buffer fluids were no longer able to maintain the required seal chamber environment.
Special Components for API Plans 53B and 53C
API Plans 53B and 53C use a bladder accumulator and piston accumulator respectively to maintain the required barrier fluid pressure. These additional components add some troubleshooting complexity. If you’re having problems maintaining the correct barrier fluid pressure you’ll need to look at the source of charging gas (53B) or the piston operations and differential pressure indicator/transmitter (53C) that could be the source of the problem.
Added Complexity for API Plans 54 and 55
Both API Plans 54 and 55 are custom-engineered solutions. They include pumps and reservoirs and a wide range of optional components such as strainers, heat exchangers, and pressure and flow control valves that fine-tune performance to the needs of the pumping process.
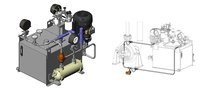
Many of the same troubleshooting guidelines mentioned above also apply here, but the added complexity of these plans can challenge even the most experienced maintenance professionals in isolating problems. When planning and installing either of these plans, ensure they are easily accessible and maintenance personnel can work unimpeded by surrounding infrastructure.
Atmospheric Side Mechanical Seal Support Troubleshooting
This category is relatively simple in number and in design. These plans provide a clean quench to a single atmospheric side seal to prevent process fluid icing or coking. The clean quench can be water, steam, or plant nitrogen. In addition to issues with tubing, connections, and instrumentation, look for a depleted level of quench fluid in the reservoir for API Plan 51. And for API Plan 62 troubleshooting, ensure that plant water, steam, or nitrogen is being supplied consistently.
To Minimize Troubleshooting, Begin With Good Design
Troubleshooting is part of every maintenance professional’s job, but you shouldn’t get bogged down in troubleshooting recurring problems associated with outdated mechanical seal support systems. Replacing outdated or inadequate components can boost reliability and lower your maintenance costs. In some cases, the best solution is a complete replacement with a mechanical seal support system that is designed to meet specific pumping requirements.
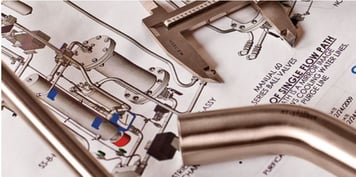
Swagelok has decades of experience working with refineries in consulting on-site to assess the specific mechanical seal support system requirements. That hands-on consultation allows Swagelok to develop detailed CAD drawings of the proposed system for your review and approval. We’ll fabricate and thoroughly test the system in our Fremont facility following ISO 9001 guidelines. The result—fast turnaround, from consultation to delivery, of the highest quality mechanical seal support systems configured to your requirements and backed by Swagelok’s Lifetime Warranty. And being local, Swagelok is available for follow-up technical support, on-site or by phone.
Need help finding the right solutions for the mechanical seal support systems you’re troubleshooting? Swagelok Northern California has helped Bay Area refineries improve the centrifugal pump reliability by providing expert consultation and Assembly Services, contact our team today by calling 510-933-6200.