Is Your Sample Probe Wake Frequency Calculation Missing Something?
by Morgan Zealear, on 9/23/20 8:45 AM
Imagine the range of outcomes when a sample probe, such as a thermowell, breaks within the fluid stream. In the best case, the result is leakage of process fluid, process shut down, and replacement of the thermowell and probe. In the worst case, you have high-pressure leakage of toxic fluids or high-temperature fluid leakage that imperils personnel working nearby, downstream damage to a pump, significant downtime, and costly repairs.
And, if you are in Northern California, it gets even worse: potential sanctions and related legal fees. You can bet that you will be hearing Cal/OSHA or the BAAQMD—possibly both. But when you have increased process pressures or flows, changes to more corrosive or viscous process fluids, or increased particulate concentrations that take a toll on sample probes, you may not even be aware of the risk.
While you might be tempted to make a quick fix and grab a replacement thermowell from the stockroom, a better approach to avoid potentially costly failures would be to ensure your replacement probe matches the current process conditions.
Sample Probe Wake Frequency Calculations Are Complex
Achieving that goal begins with a sample probe wake frequency calculation based on static and dynamic stresses relative to process temperature and pressure. Flow-induced vibration, for instance, can lead to fatigue failures. And erosion from particulates weakens probe integrity. You want to avoid both with the correct calculations.
The ASME PTC 19.3 TW-2016 Standard explains the sample probe wake frequency calculations in detail. But, before you dig in, you may wonder how complex are they?
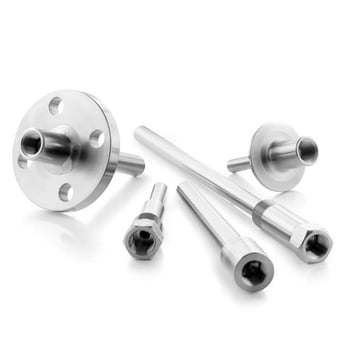
Well, using a thermowell as an example, factors such as wall thickness, unsupported length, root and tip diameter, process fluid velocity, and thermowell natural frequency, as well as criteria such as Strouhal Frequency and Reynolds Number may all be part of the calculation. From a practical standpoint, calculating sample probe wake frequency under a range of process conditions is the shared domain of instrument engineers and process engineers.
When You Don’t Have In-House Engineering Expertise
If you have the process and engineering expertise in-house, you’re welcome to do the sample probe wake frequency calculations to determine the optimum sample probe design. A simpler approach is to work with a local fluid systems vendor who has considerable experience with sample probe wake frequency calculations. An experienced vendor will not only handle the calculation, but they’ll also provide valuable guidance regarding other design factors to improve reliability as well as optimize performance. Some of the critical factors to consider include:
- Shorter, heavier diameters stiffen the probe and increase resonant frequency
- Tapered thermowells reduce vibration amplitude, but the increased thermal mass slows response time
- Attachment designs: flange, lap flange, threaded, through-hole welded, or welded per DIN 43772
Depending on the process, piping geometry, and sampling requirements, your fluid system vendor may also make recommendations regarding probe orientation. The installation angle can reduce forces acting on the probe, improve accessibility, or increase exposure to flow to provide more accurate readings. For example, installed in an elbow, a thermowell pointed upstream creates a laminar flow over the tip and reduces the stream force acting on it.
Understand Process And Materials For Best Probe Design
Understanding process conditions, flow-induced stresses acting on a sample probe, and material characteristics is critical to designing and installing probes suited to the specific process applications. For many processes, not only are thermowells critical to monitoring process conditions, but they are also an essential part of the pressure containment envelope. Failure can be catastrophic—toxic leakage, fire, or even explosion—if not immediately detected.
In high-velocity processes requiring high-strength piping and elevated fluid velocities, sample probe design and installation is all the more important. Whenever you’re installing a thermowell, whether a replacement or a brand new installation, it’s well worth the time to ensure the sample probe wake frequency calculation is done correctly. An experienced fluid systems vendor will take into account the process conditions and material characteristics of the probe to ensure continued reliability and performance.
Swagelok, Your Local Fluid Systems Expert
Swagelok is your expert source for helping refineries in Northern California design, install, and maintain fluid systems critical to their operations. Our Field Engineers and certified technicians apply decades of experience in solving unique fluid processing challenges. A consultation relieves you of the complexities of sample probe wake frequency calculations and ensures your sample probe designs support safe, cost-effective operations.
To learn how Swagelok Northern California can help you with the complexities of sample probe wake frequency calculations and ensure probes are designed to meet your specific process requirements, contact our team today by calling 510-933-6200.
Morgan Zealear | Product Engineer – Assembly Services
Morgan holds a B.S. in Mechanical Engineering from the University of California at Santa Barbara. He is certified in Section IX, Grab Sample Panel Configuration, and Mechanical Efficiency Program Specification (API 682). He is also well-versed in B31.3 Process Piping Code. Before joining Swagelok Northern California, he was a Manufacturing Engineer at Sierra Instruments, primarily focused on capillary thermal meters for the semiconductor industry (ASML).