Share this
Designing For Weld Perfection
by Jeff Hopkins on 9/12/18 9:12 AM
How do the methods of increasing purity come into play when orbital welding is used?
Swagelok's orbital welding system offers precision and control combined with easy-to-use touch-screen operation and real-time monitoring and recording.
We have looked at 316 stainless steel in high-purity systems and reactive chemistry and how the purity can be increased through chemical passivation and/or electro-polishing. How do those methods come into play when orbital welding is used?
Orbital welding in many ways has become the gold standard in high-purity fluid system construction. Good quality welds can make a huge difference when it comes to system performance and starting with the right alloy composition on both sides of the butt-weld is paramount.
One of the primary factors for weld quality is the sulfur content of the metal. Equal amounts of sulfur on either side of the weld can make a huge difference in overall weld quality. At Swagelok, we tightly control our sulfur, chromium, and nickel content to ensure maximum weld repeatablility.
316L SS: ASTM vs. Swagelok
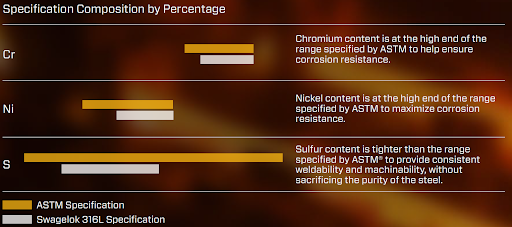
Mis-matches in sulfur can lead to welds that don't fully penetrate the walls of both sides of the tubing. Improper welds like this can create dead volumes and entrapment zones and result in a weld bead shift. A semiconductor-quality weld bead should be neither concave nor convex and be nearly indistinguishable after post-weld passivation.
Passivation is, for the most part, the only option after welding to clean up a system. Why? Electro-polishing requires placing an electrode on both sides of the metal for zonal surface treatment. In most systems, after welding the components together it's basically impossible to get an electrode to the inside components.
Passivation is typically an immersion of the parts into a nitric/hydrofluoric acid mixture for about 30 minutes to remove those pesky surface ions created during welding. If your system has female VCR fittings, you need to consider the anti-galling treatment on the female VCR nuts. Swagelok's anti-galling treatment is a thin layer of silver with a light lubricant on the female threads of the nut. Immersion into a strong acid solution will completely etch away the silver and can actually contaminate the weldment.
To solve this problem, Swagelok has a solution: removable split VCR nuts. This enables the weldment to be effectively passivated without the nuts on the assembly. Still concerned that the silver and subsequent lubricant will contaminate your system? Swagelok also offers our female VCR nuts with no sliver and/or no lubricant. Of course, removal of the lubricants can create the potential of galling when pulling up the VCR fitting.
(Prefer to talk live? Please give us a call at 510-933-6200.)
- Swagelok Welding Systems (product page)
- Beyond Basics: Swagelok's Advanced Class In Orbital Welding (blog article)
-
With Proper Training, Orbital Welding Leads the Way (blog article)
Share this
- Archive (465)
- Assembly Services (207)
- About (100)
- Seal Support Systems (96)
- Best Practices (82)
- Training Services (74)
- Fittings (51)
- Semiconductor Applications (49)
- Hoses and Flexible Tubing (47)
- Regulators (44)
- Tubing (42)
- Grab Sampling Systems (32)
- Sampling Systems (32)
- Gas Systems (30)
- Services (30)
- Downloads (29)
- Valves (24)
- Orbital Welding (17)
- Application Support (15)
- Case Studies (13)
- Steam Systems (13)
- Frequently Asked Questions (12)
- Tools (12)
- Measurement Devices (7)
- Subsystems (6)
- Thermal Management (6)
- September 2023 (1)
- August 2023 (2)
- June 2023 (1)
- March 2023 (3)
- February 2023 (3)
- January 2023 (4)
- December 2022 (4)
- November 2022 (4)
- October 2022 (4)
- September 2022 (1)
- August 2022 (3)
- July 2022 (2)
- June 2022 (4)
- May 2022 (1)
- April 2022 (2)
- March 2022 (1)
- February 2022 (2)
- January 2022 (3)
- December 2021 (1)
- November 2021 (6)
- October 2021 (6)
- September 2021 (8)
- August 2021 (4)
- July 2021 (3)
- June 2021 (6)
- May 2021 (6)
- April 2021 (7)
- March 2021 (5)
- February 2021 (4)
- January 2021 (6)
- December 2020 (5)
- November 2020 (6)
- October 2020 (6)
- September 2020 (8)
- August 2020 (7)
- July 2020 (8)
- June 2020 (8)
- May 2020 (6)
- April 2020 (9)
- March 2020 (7)
- February 2020 (10)
- January 2020 (21)
- December 2019 (23)
- November 2019 (21)
- October 2019 (22)
- September 2019 (21)
- August 2019 (22)
- July 2019 (23)
- June 2019 (20)
- May 2019 (23)
- April 2019 (22)
- March 2019 (21)
- February 2019 (20)
- January 2019 (21)
- December 2018 (14)
- November 2018 (19)
- October 2018 (23)
- September 2018 (17)
- August 2018 (29)
- July 2018 (11)
- June 2018 (6)
- May 2018 (5)
- April 2018 (4)
- March 2018 (5)
- February 2018 (3)
- January 2018 (3)
- December 2017 (2)
- November 2017 (4)
- October 2017 (3)
- September 2017 (2)
- August 2017 (6)
- July 2017 (4)
- June 2017 (4)
- May 2017 (4)
- April 2017 (3)
- March 2017 (4)
- February 2017 (3)
- January 2017 (3)
- December 2016 (3)
- November 2016 (3)
- October 2016 (3)
- September 2016 (5)
- August 2016 (5)
- July 2016 (4)
- June 2016 (5)
- May 2016 (3)
- April 2016 (4)
- March 2016 (5)
- February 2016 (11)
- January 2016 (1)
- December 2015 (3)
- November 2015 (4)
- October 2015 (3)
- September 2015 (4)
- August 2015 (4)
- July 2015 (8)
- June 2015 (5)
- May 2015 (3)
- April 2015 (4)
- March 2015 (4)
- February 2015 (3)
- January 2015 (4)
- December 2014 (2)
- November 2014 (3)
- October 2014 (4)
- September 2014 (4)
- August 2014 (4)
- July 2014 (5)
- June 2014 (4)
- May 2014 (4)
- April 2014 (5)
- March 2014 (4)
- February 2014 (3)
- January 2014 (4)
- December 2013 (5)
- November 2013 (3)
- October 2013 (4)
- September 2013 (3)
- August 2013 (5)
- July 2013 (5)
- June 2013 (5)
- May 2013 (3)
- April 2013 (6)
- March 2013 (4)
- February 2013 (4)
- January 2013 (8)
- December 2012 (4)
- November 2012 (6)
- October 2012 (6)
- September 2012 (4)
- August 2012 (4)
- July 2012 (4)
- June 2012 (4)