Cleaning, Corrosion Resistance, And Fluid System Integrity
by Jeff Hopkins, on 8/22/19 9:00 AM
How pure do you really need your components? We have a process for every level
"In vacuum work, cleanliness is absolutely essential. All tubing used
should be degreased and then dried thoroughly. If this is not done, oils and moisture may vaporize as pressure is reduced and the system will appear to leak even though it is tight."
- From Swagelok Tube Fitter's Manual
Here is a fun experiment you can do at home:
Buy a bottle of distilled water from the grocery store or fill a clean water bottle with water from your DI water system (if you have one).
- Put the bottled water in the freezer overnight.
- The next day, check on the water to see if it’s frozen. If the initial conditions were right the water should still be in the liquid phase.
- Open the bottle and drop a grain of sand or small pebble into the water and watch the whole bottle flash freeze!
This happens because water needs an initial crystal structure from which the ice can begin to form, even when it is well below the freezing point. Once the structure is introduced, a cascade crystallization reaction will occur, changing the phase of the water.
Purity can have a dramatic impact on a fluid system's product yield and performance. Surface finishes, thread sealants, lubricants, coatings, and chemical composition of the system materials all can affect system performance. Impurities can result in all manner of strange system behavior.
Cleaning specifications
Purity matters a lot when it comes to chemical manufacturing and coating processes such as Chemical Vapor Deposition (CVD), Physical Vapor Deposition (PVD), Epitaxy (MBE or ALE), Atomic Layer Deposition (ALD), and many other processes. Swagelok has worked closely with national laboratories, academic organizations, and private partners to develop cleaning processes, material chemistries, and surface treatments and coatings to meet the demands of the most challenging applications.
Let’s explore some of these treatments and how they can help you with your process challenges:
SC-01 Ultrahigh-Purity (UHP) Process Specification:
When you need something as clean as possible,
it's hard to beat the multiple techniques of Ultrahigh-Purity cleaning. First, the base metal has to be of appropriate quality and chemical purity with carefully controlled levels of sulfur and carbon. Other contaminants are removed from the base metal using techniques such as Vacuum Induction Melting (VIM) and Vacuum Arc Re-melting (VAR).
Once the base metal is purified the fluid system components can be fabricated, being cut and then carefully polished to a nearly mirror-like surface finish. After that, the components are degreased from cutting fluids and immersed in an acid bath to remove all surface ions and iron in a process called passivation. Then, the components are put into a chemical bath, and an electric current is used to further passivate the components resulting in a mirror shine surface called electro-polishing. Passivation and electro-polishing results in a surface that is almost entirely chromium. SC-01 is the king of clean.
SC-11 Special Cleaning and Packaging:
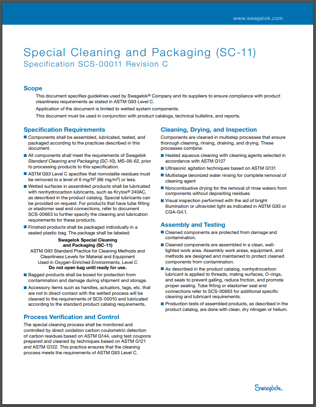
If the process needs to be clean but not necessarily ultra-clean, then SC-11 may be in the cleaning for you. SC-11 complies with ASTM G93 Level C to ensure that non-volatile residues from things such as cutting lubricants are cleaned to a very low level. Furthermore, lubricants used on the components which aid assembly and protect against galling are specifically non-hydrocarbon based. This is particularly critical for oxygen rich services at 30 percent or greater concentration. When oxygen is at elevated levels, the auto ignition point of flammable materials is dramatically reduced. Relatively benign operations such as pressurizing a system or increasing the flow of gas can result in compression-ignition of hydrocarbon lubricants resulting in an explosion. At high temperatures the base metal of a system can ignite with concentrated oxygen. In fact, this is the operational principal of a cutting torch or burning bar (thermal lance).
SC-10 Standard Cleaning and Packaging:
For many oil and gas systems and general purpose applications, Swagelok’s default cleaning process is SC-10. No special designators are required to order SC-10 components. Standard cleaning and packaging removes all oil and grease used in manufacturing, and lubricates the components with hydrocarbon or halocarbon based lubricants. Without special equipment you would never notice that the components are even lubricated. However, if you attempt to use a cheap third-party substitute fitting, you may find that the part galls to itself almost immediately and you’re running to the store to buy another one. A young entrepreneur came to our will-call recently because he had purchased several low cost tube fittings from a hydraulic components supplier, only to spend days cutting them out of the system because of galling and poor sealing. When you’re looking to be lean with your cash, be wary of buying something because the price looks right. Often you’ll wind up spending way more than you wanted on recovery.
SC-06 Standard Cleaning and Packaging:
For photovoltaic (PV) cell manufacturing, Swagelok developed a cleaning specification that is slightly less stringent than the SC-01 UHP process. SC-06 may be right when specific surface chemistry is of a lesser significance, and when it may not be important to passivate/electro-polish interior surfaces of the fluid system component. Like SC-01 there are absolutely no lubricants or coatings on the finished parts and they are individually bagged. Unlike UHP components, it is not as critical to assemble SC-06 components in a clean room.
Inert, chemically compatible, corrosion resistant coatings
Corrosive and caustic process chemistries at times are not compatible with 316 stainless steel components. Usually this is reason to change the base metal to a nickel alloy or other metal like aluminum or brass alloys. At Swagelok, we offer a wide variety of material options for our tube fittings shown in the chart to the right. Softer materials like 316 stainless steel, aluminum, brass, and alloy 400 are not incredibly difficult to machine; however, nickel based alloys like 600, 625, 825, and C-276 are incredibly difficult to work with and the base nickel is also more expensive, making the fittings and tubing nearly 20 times the price of stainless steel and brass.
Because of this cost, we offer fittings with the inert, chemically compatible, and corrosion resistant coatings. These specialty coatings provide excellent corrosion resistance by protecting fluid system alloy from attack in applications such as sour gas (H2S) service and can even add hydrophobic properties to the components, reducing sludge and deposits from building up on fluid system surfaces. In applications where chemistry may be compatible with Nylon or PTFE but pressure and temperature are far too high for plastics, coatings may allow you to manage system cost while preserving integrity.
Just ask
Swagelok Northern California has a great deal of exposure to all aspects of fluid system design and engineering. Whether you have a simple question or a complex challenge, we're glad to hear from you.
More like this:
- Not All Materials Pass Muster For Ultrahigh-Purity (blog)
- Swagelok Cleanliness Chain (download page)
- Swagelok Assembly Services (web page)